In mechanical design, we often use aluminum metal alloys. These metals have good strength, corrosion resistance, and workability. 7075 Aluminum vs 6061 are two of the most popular aluminum metal alloys. Their high strength-to-weight ratio makes them a good choice for non-intensive and general-purpose uses, especially for weight-sensitive locations such as high-speed motion platforms, aircraft structures, bicycle racks, etc.
While 6061 and 7075 aluminum grades are similar in some ways, there are significant differences between the two. So the question is, what is the difference between 6061 and 7075 aluminum metal? This article briefly introduces 7075 aluminum vs 6061 aluminum alloys and compares their compositions, mechanical properties, cost, applications, etc. Hopefully, it will help you choose the best alloy for your project.
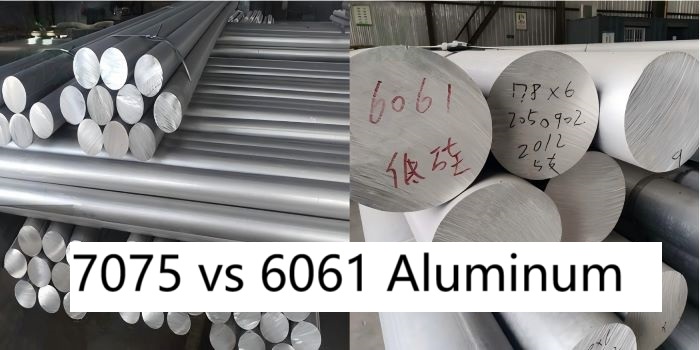
What is 6061 Aluminum Alloy?
6061 aluminum alloy is a widely used heat-treatable aluminum alloy with a combination of excellent mechanical properties, good weldability, and high corrosion resistance. It belongs to the 6xxx series of aluminum alloys, which are aluminum-magnesium-silicon alloys. The primary alloying elements in 6061 are aluminum, silicon, and magnesium.
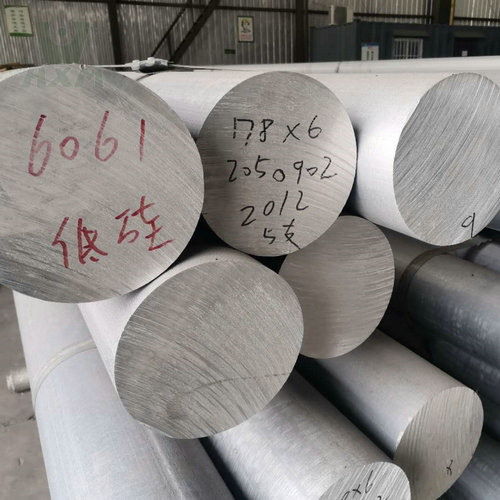
What is 7075 Aluminum Alloy?
7075 aluminum alloy is a high-strength, heat-treatable aluminum alloy known for its excellent strength-to-weight ratio and good mechanical properties. It belongs to the 7xxx series of aluminum alloys, which are aluminum-zinc-magnesium alloys. The primary alloying elements in 7075 are aluminum, zinc, and copper.
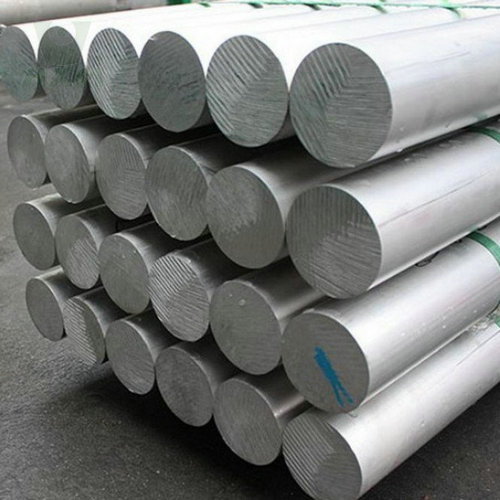
The Difference Between 7075 Aluminum vs 6061 Aluminum
Let’s compare aluminum alloys 6061 and 7075 from different perspectives, including composition, mechanical properties, cost, application, etc.
Chemical Composition of 7075 Aluminum vs 6061:
7075 aluminum alloy belongs to the 7xxx series in which zinc and copper are used as the primary alloying elements. 6061 aluminum belongs to the 6xxx class of aluminum, using magnesium and silicon as the primary alloying elements. Here is a complete breakdown of the chemical composition of 7075 Aluminum vs 6061:
Aluminum Alloy | Al | Zn | Mg | Cr | Cu | Si |
6061 | 97.90% | — | 1.00% | 0.20% | 0.28% | 0.60% |
7075 | 90.00% | 5.60% | 2.50% | 0.23% | 1.60% | — |
Interested in specific alloy specs? Contact us now for datasheets and aluminum alloy quotes.
Mechanical Properties of 7075 Aluminum vs 6061:
In terms of strength, 7075 aluminum far exceeds 6061 aluminum. Its higher tensile strength makes it ideal for high-stress structural applications such as aircraft frames.
Type 6061 Aluminum Alloy | Type 7075 Aluminum Alloy | |||
Metric | English | Metric | English | |
Yield strength | 276 MPa | 40,000 psi | 503 MPa | 73,000 psi |
Modulus of Elasticity | 68.9 GPa | 10,000 ksi | 71.7 GPa | 10,400 ksi |
Thermal conductivity | 167 W/m-K | 1160 BTU-in/hr- ft²-°F | 130 W/m-K | 900 BTU-in/hr-ft²-°F |
Melting point | 582 – 652°C | 1080 – 1205°F | 477 – 635°C | 890 – 1175°F |
Electrical resistivity | 3.99 x 10-6 ohm-cm | 5.15 x10-6 ohm-cm | ||
Hardness (Brinell) | 95 | 150 | ||
Machinability | Good | Fair |
If your application requires extreme strength, 7075 aluminum is a better choice. For general use, 6061 aluminum offers a good balance between strength and machinability.
Characteristics of 7075 Aluminum vs 6061:
6061:
- Good weldability.
- Moderate strength and excellent corrosion resistance.
- Suitable for a wide range of applications, including structural components and machinery parts.
7075:
- High strength, particularly in comparison to 6061.
- Lower corrosion resistance compared to 6061.
- Often used in applications requiring high strength-to-weight ratios, such as aircraft and aerospace components.
6061 aluminum has excellent corrosion resistance, especially in marine environments, making it ideal for outdoor or moist conditions. 7075, while strong, is more susceptible to corrosion and requires surface treatment or protective coatings.
In terms of weldability, 6061 is far easier to weld compared to 7075 aluminum alloy, which is generally not recommended for welding due to cracking issues.
Need marine-grade aluminum alloy materials? Inquire now about our 6061 stocks!
Cost of 7075 Aluminum vs 6061: Which Is More Affordable?
6061:
- Generally less expensive than 7075.
- More widely available and used in various industries, contributing to its lower cost.
7075:
- Due to its higher strength and specific applications, 7075 is usually more expensive than 6061.
- Commonly chosen when high strength is a critical factor.
Want an exact quote? Request aluminum alloy pricing today!
Applications of 7075 Aluminum vs 6061:
6061 Aluminum Metal Alloy | 7075 Aluminum Metal |
---|---|
Building products | Aircraft wings and fuselages |
Electrical products | Missile parts |
Piping | Gears and shafts |
Bicycle frames | Worm gears |
Furniture | Regulating valves |
Automotive parts | Fuse parts |
At Huaxiao Metal, we help clients across industries select the right aluminum alloy material based on mechanical needs, environment, and cost.
Weldability: The Major "No" for 7075:
6061: Can be readily welded using various techniques.
7075: It is not recommended for welding. The heat causes it to become brittle and highly susceptible to cracking, compromising the integrity of the joint. For assemblies, mechanical fastening (bolts, rivets) is required.
Corrosion Resistance & Stress-Corrosion Cracking (SCC)
- 6061: Exhibits good general corrosion resistance.
7075: Is significantly more susceptible to corrosion, especially Stress-Corrosion Cracking (SCC). This means that under tensile stress in a corrosive environment, cracks can form and propagate, leading to sudden failure. Proper surface treatment (anodizing, painting) is mandatory for durability.
The Core Decision: When to Choose 7075 Over 6061?
Answer these questions to make a quick decision:
Is maximum strength-to-weight ratio your absolute number one priority?
- Yes? -> You need 7075.
Does your application require welding for assembly?
- Yes? -> You must use 6061. 7075 is generally not weldable.
Is your component exposed to a corrosive environment without robust surface protection?
- Yes? -> 6061 is the safer, more resistant choice.
Is the budget a primary driver for a standard structural application?
- Yes? -> 6061 offers the best performance-per-dollar.
Are you designing a high-stress, critical component like an aircraft frame, a mold, or high-performance sporting goods?
- Yes? -> The strength of 7075 is likely necessary.
Sourcing High-Performance Alloys from Huaxiao Metal
Whether you need the versatile 6061 or the peak-performance 7075, Huaxiao Metal has the inventory and expertise to deliver. We provide certified materials that meet the stringent demands of the aerospace, defense, and industrial sectors.
Certified Materials: Full traceability and certification (e.g., ASTM B209, AMS-QQ-A-250/12).
Precision Cutting: We supply cut-to-size plates and bars to your exact specifications.
Expert Consultation: Our team can help you validate your material choice.
Get a competitive quote for your specific material needs.
Frequently Asked Questions (FAQ)
Can I use 7075 for a marine application?
It is highly discouraged. 7075’s poor corrosion resistance makes it unsuitable for saltwater environments, even with coating. 6061 or, more ideally, a 5xxx series alloy (like 5083) would be a much better choice.
What is 7075-T651? What does the "T651" mean?
T651 is a specific temper for 7075. It means the alloy has been solution heat-treated, stress-relieved by stretching, and then artificially aged. This process reduces internal stresses from manufacturing, improving dimensional stability during machining, which is critical for thick plates.
For CNC machining, which is better, 6061 or 7075?
Both machine well, but 7075 is often preferred for high-speed CNC work as it produces smaller, more manageable chips and can result in a superior surface finish. However, 6061 is less abrasive on cutting tools.
In Conclusion:
From the above differential comparison analysis, it can be concluded that both alloys have a high strength-to-weight ratio and are good choices for non-intensive general-purpose applications. However, each of them excels at specific uses, depending on intended use and budget.
Aluminum 6061 would be a better choice when the product needs to be welded or formed, requires moderate to high tensile strength, or corrosion is a concern. It’s also a better option for extruding complex shapes or when you’re on a budget.
The main characteristic of 7075 aluminum is its very high strength. Therefore, it is more suitable when extremely high tensile strength is required, along with a high strength-to-weight ratio and high fatigue resistance.
Ready to buy or need a quote? Contact Huaxiao Metal now to consult prices, stock, and specifications for 7075 and 6061 aluminum alloys!