In recent years, the global environment has faced more severe challenges, and it is imminent to improve motor efficiency and reduce motor loss. In addition, with the rise of new mobile technologies, the use environment and specification requirements of motors have also changed, requiring smaller motors with higher power output. In order to meet these requirements, increasing the rotation speed of the motor has become a solution, and even for small motors, the output power can be increased by increasing the rotation speed. However, as the speed increases, the iron loss of the motor core will also increase sharply, resulting in a decrease in efficiency.
The motor core is usually made of non-oriented electrical steel plate, and the standard plate thickness is 0.5 mm and 0.35 mm. This material is selected because the high-speed rotation of the motor is related to the high frequency of the magnetic field in the iron core, and the iron loss of the electrical steel plate will increase with the increase of frequency. This is mainly due to eddy current losses. Eddy’s recent loss can be expressed by the square of the frequency, magnetic flux density, and plate thickness.
In order to suppress the increase in iron loss caused by frequency, people have developed ultra-thin electrical steel sheets, which can greatly reduce the increase in eddy current loss relative to frequency while maintaining the high saturation magnetic flux density and other characteristics of non-oriented electrical steel sheets. It is reported that ultra-thin electrical steel sheets are manufactured by re-rolling existing non-oriented electrical steel sheets. The development of this ultra-thin electrical steel sheet is expected to play an effective role in fields such as small high-speed electric motors.
However, there are still difficulties in making wide-width ultra-thin electrical steel sheets, and how to effectively use ultra-thin electrical steel sheets to manufacture large-scale motor cores has become an issue. For this reason, people have developed an extremely thin electrical steel strip coil core called “wound laminated core”, which can achieve the goal of large-scale motor cores even if the width is narrow. This type of iron core has a plate thickness of only 0.08mm, which is very thin and can be made into a coiled shape. By increasing the number of windings, it can achieve a larger size relative to the radial direction.
In general, a “wound core” refers to a core produced by winding an existing electrical steel sheet, while a “wound laminated core” refers to a core produced by winding an ultra-thin electrical steel strip with a thin plate thickness. This type of core maintains interlayer insulation by winding an extremely thin electrical steel strip with an insulating coating.
At present, although a method of winding an iron core with a thinner amorphous material has been developed, the interlayer insulation performance of the iron core cannot be maintained because the amorphous material itself has no insulating coating. In contrast, wound laminated cores are wound using extremely thin electrical steel strips with insulating coatings, so that interlayer insulation can be maintained.
Researchers such as Wakabayashi Daisuke of the University of Arts and Sciences in Japan studied the changes caused by the core structure by comparing the structure of the wound laminated core and the traditional laminated core. At the same time, by evaluating wound laminated cores made of ultra-thin electrical steel strips of different thicknesses, the optimal thickness and manufacturing conditions for further reducing iron loss were explored.
They believe that the wound laminated core made of the newly developed ultra-thin electrical steel strip has magnetic properties comparable to conventional laminated cores. By increasing the number of windings, radial size can be achieved, which contributes to the reduction of loss and size of high-speed rotating electrical machines.
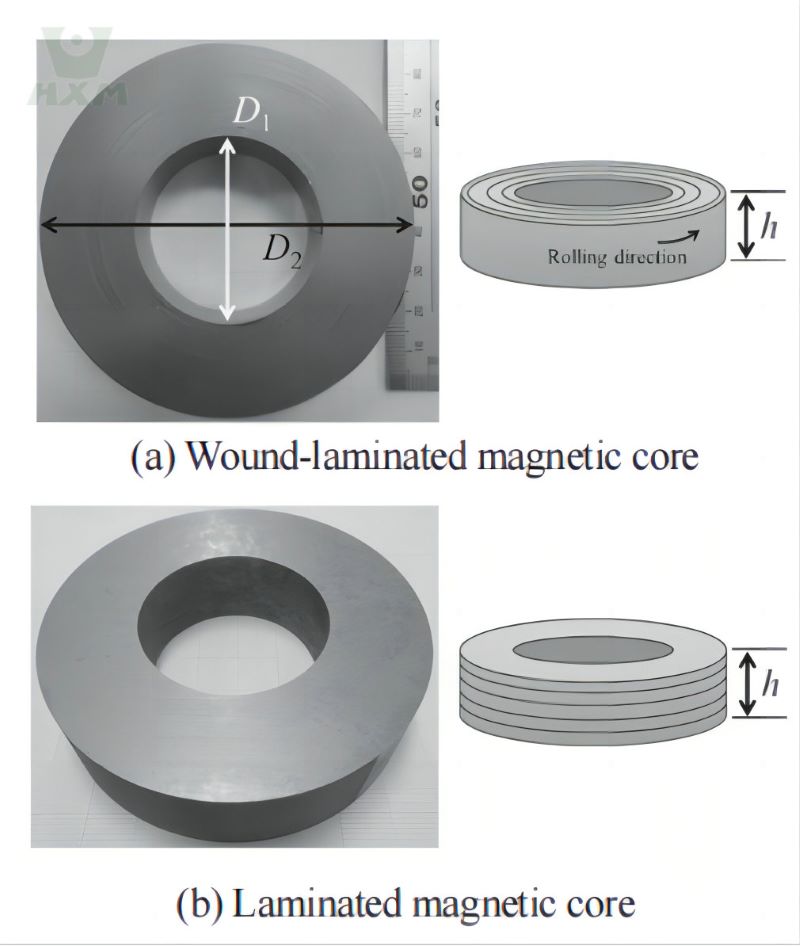
Therefore, people can provide iron cores of different sizes, further expanding the range of effective utilization of ultra-thin electrical steel sheets. In particular, the laminated core with a plate thickness of 0.08mm can maintain the characteristics of low iron loss and high magnetic permeability in the frequency range of 50Hz to 1kHz and is the most suitable core material for reducing hysteresis loss and eddy current loss.
In the frequency range above 1kHz, due to the increase of eddy current loss, the material selection of 0.05mm can be considered. The researchers said they plan to process the laminated iron core made of extremely thin electrical steel strips into the shape of a motor stator to further clarify the characteristics of the stator and its effect on motor applications.
Definition of Electrical Steel
Electrical steel, also known as silicon steel, is an indispensable and important soft magnetic alloy in the electric power, electronics, and military industries, and is also the metal functional material with the largest output. It is mainly used as the iron core of various motors, generators, and transformers. Its production process is complicated and the manufacturing technology is strict. Foreign production technologies are protected in the form of patents, which are regarded as the life of the enterprise.
Electrical Steel Overview
Electrical steel has a history of hundreds of years. Electrical steel includes two types: electrical steel with Si <0.5% and silicon steel with Si content of 0.5~6.5%. It is mainly used as the core of various motors, transformers and ballasts. It is an important part of electric power, and electronics and An important soft magnetic alloy that is indispensable in the military industry. Electrical steel is the largest used magnetic material and is also an important energy-saving metal functional material.
The manufacturing process and equipment of electrical steel, especially grain-oriented silicon steel, are complex, the composition is strictly controlled, the manufacturing process is long, and there are many factors that affect performance. Therefore, the quality of grain-oriented silicon steel products is often regarded as an important indicator of a country’s special steel manufacturing technology level. , and won the reputation of “art product” among special steels.
Electrical Steel Performance Requirements
Low Core Loss (PT):
Core loss refers to the ineffective electric energy consumed when the core is magnetized under an alternating magnetic field of ≥50Hz, referred to as iron loss, also called alternating loss, and its unit is W/kg. This kind of ineffective electric energy consumed due to various obstacles to the change of magnetic flux not only loses electric energy through the heating of the iron core but also causes the temperature rise of the motor and transformer. The iron loss (PT) of electrical steel includes three parts: hysteresis loss, eddy current loss (Pe), and abnormal loss (Pa).
Electrical steel plates have low iron loss, which can not only save a lot of electrical energy, but also extend the operating time of motors and transformers, and simplify cooling devices. Since the power loss caused by the iron loss of electrical steel plates accounts for 2.5% to 4.5% of the annual power generation in various countries, countries producing electrical steel plates always try every means to reduce iron losses and use iron loss as the most important indicator to evaluate the magnetic properties of products. The iron loss value of the product is used as the basis for classifying product brands.
High Magnetic Induction Intensity (B):
Magnetic induction intensity is the number of magnetic force lines passing through the unit cross-sectional area of the iron core, also called magnetic flux density. It represents the magnetizing ability of the material, and the unit is T. The magnetic induction intensity of the electrical steel plate is high, the excitation current (also called no-load current) of the iron core is reduced, and the copper loss and iron loss are reduced, which can save electric energy.
When the power of the motor and transformer remains unchanged, the magnetic induction intensity is high, the design Bm can be increased, and the cross-sectional area of the iron core can be reduced, which reduces the volume and weight of the iron core and saves the number of electrical steel plates, wires, insulation materials, and structural materials. It can reduce the total loss and manufacturing cost of motors and transformers and is beneficial to the manufacturing, installation, and transportation of large transformers and large motors.
The design Bm of grain-oriented silicon steel is as high as 1.7~1.80T, which is close to the B8 value, so B8 is used as the guaranteed magnetic induction value. The design Bm of the motor is about 1.5T, which is close to the B50 value of cold-rolled non-oriented electrical steel. Therefore, B50 is used as the guaranteed magnetic induction value of cold-rolled non-oriented silicon steel. The magnetic induction of hot-rolled silicon steel is lower, and B25 is usually used as the guaranteed value.